Your process requires a sterile end product. To achieve this, you plan on installing a sterilizing filter. But with so many choices, how do you choose the best one?
Some suppliers offer single-layer membrane sterilizing filters. Others may offer filters with two layers of membrane, sometimes with different pore sizes (a larger pore size in front of the final sterilizing filter), or two layers of identical material in the same pore size. Each plays a specific role in reaching your sterilizing requirements. This article will discuss the many factors in choosing a sterilizing filter and list our products that deliver targeted retention.
Factors to be considered
Level of Sterilization
The first and most important factor is what level of sterilization is required. Are you looking to remove bacteria only? Is mycoplasma removal required? Is endotoxin contamination a concern? The answers to these questions will determine the pore size and filter type required for your application.
Basic bacteria removal can be achieved with an 0.2 or 0.22 micron (different manufacturers tend to use these ratings interchangeably - the most important factor is that it is validated for bacteria retention).
For mycoplasma removal, a smaller pore size is required - 0.1 or even 0.03 microns depending on the manufacturer and validation testing. Where endotoxin removal is also required, a positively charged version of these filters is needed.
How Sterilizing Filters are Validated
Sterilizing filters should be validated using test procedures that comply with ASTM F 838-15(ae1) protocols for the determination of bacterial retention in filters used for liquid filtration. The challenge level is a minimum of 107 organisms per cm2 of filter media. CPF filters have > 7-log removal when challenged with the organisms listed below (0.03μm, 0.10μm, and 0.22μm meet the FDA definition of sterilizing grade filters).
Pore Size | Organisms Used to Validate |
0.03μm | Acholeplasma laidlawii |
0.10μm | Brevundimonas diminuta |
0.22μm | Brevundimonas diminuta |
Fluid Characteristics
After deciding what pore size rating and filter type are required, certain fluid characteristics need to be accounted for in order to pick the best filtration solution.
The chemical composition of your process fluid may limit the choice of membrane materials. For aqueous solutions, Polyethersulfone is usually the best choice due to its high flow rate and dirt-holding capacity. For other fluids that may negatively affect PES, Nylon 6,6 membrane would be a better choice.
If the fluid is known to be low in particulate contamination and has a fairly low bacteria count a single layer membrane filter will probably suffice. In critical applications requiring extra security, a double layer of the same pore size rating could be a better choice.
For fluids with low particulates but higher bacteria count, a dual layer membrane filter with a larger pore size up front (for example 0.45 micron followed by 0.22 micron) could help extend the life of the sterilizing layer.
For fluids with high particulate load, a higher capacity prefilter can be incorporated in front of the final sterilizing layer.
Flow Rate, Batch Size, Filter Longevity
Other factors are required flow rate, batch size and expected filter life. For low flow or low volume requirement, the choice may not matter very much, but where these are important considerations, the choice can make a huge difference.
A single layer filter will generally provide the highest flow rate per cartridge, but depending on the fluid characteristics discussed above, could result in premature fouling and shortened service life.
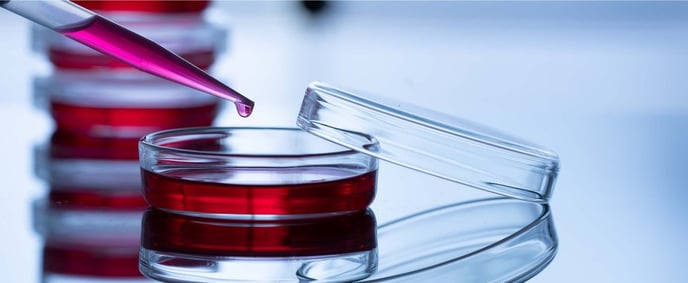
Adding an integrated prefilter will reduce flow rate per cartridge, but the trade off could be worth it if service life is extended to meet batch size requirements. The reduced flow can also be offset by using a longer cartridge or capsule - 20” or 30” instead of a basic 10” - or multiple cartridges in the same housing.
Integrity Testing & Pre-sterilization
All sterilizing filters must be 100% integrity tested by the manufacturer prior to quality release. In addition, the integrity test release criteria must be validated for bacteria and or mycoplasma removal, typically following ASTM F838 protocols as mentioned above.
In some cases, it may be desirable to purchase pre-sterilized filters. This eliminates the need for sterilizing the filters after installation. This normally applies to capsule filters which retain sterility after opening as long as they are handled and installed appropriately. Cartridge filters are not normally supplied pre-sterilized as opening the packaging (usually plastic bagging) will most likely negate the sterilization no matter how carefully the cartridges are handled.
There are several methods employed to pre-sterilize filters. The most common is gamma radiation after packaging.
Filter Quality & Materials of Construction
Materials used to manufacture sterilizing filters must be carefully selected and controlled to make sure they meet applicable quality and regulatory requirements. All materials must be non-toxic and meet USP Class VI and other toxicology requirements. In addition, the filters must not contain extractable substances that could alter or contaminate the fluid being filtered. This includes proper selection of raw materials, manufacturing equipment, and area cleanliness to protect the filters from the surrounding environment.
Vendor Specialization
There are scores of sterilizing filters on the market today. Their construction will vary by materials used, manufacturing processes, country of origin, quality, pore sizes, and type and size of the device.
You can purchase sterilizing filters from a variety of sales channels – manufacturer direct, distributors, procurement sites, and catalog houses.
Prices can vary greatly, with the most expensive sold by large manufacturers carrying high R&D costs, and the least expensive sold by high volume, offshore manufacturers that lack support and oftentimes product consistency. Critical Process Filtration is a middle-of-the-pack vendor that provides first-quality, proven, reliable filters and technical support to all its customers.
Lead times are just as wide-ranging. All channels depend on manufacturing output, and in 2022 that challenge depends on many factors. While every buyer wants product delivery that meets their production schedule, choosing the right product & quality should always be the priority to avoid costly mistakes in your own production environment. That said, when you find the right product, why wait longer than necessary?
Support & Testing
You have identified your filtration goals and what you know about the fluid(s) to be filtered. How do you decide among the options available? That’s where Critical Process Filtration can help. Unlike other vendors, CPF manufactures all of the variations described above, so we will recommend the sterilizing filter that is best for your application, rather than just one we happen to sell.
If your process goals and fluid are well characterized (flow rate, batch size, particle, and bacteria load, etc.), we can often make a recommendation based on the information you provide. Where there may be information gaps, many times a short conference call with CPF Applications specialists can narrow down the choices and point to the best option. If necessary, our Applications team can perform filtration tests using your process fluid, either in our Applications Lab or at your facility.
Typical Example of Why Filtration Support Matters
A customer was using a sterilizing filter in their process but was experiencing premature fouling, preventing the completion of a batch without having to change and re-sterilize their filter train. They did not wish to invest in new equipment and plumbing to increase the size of their filtration system and were looking for alternatives. After a call between the customer’s operations team and CPF Applications, the customer submitted a sample of their process fluid for filterability testing, along with a clogged filter for analysis.
Microscopic examination of the membrane from the clogged filter showed the presence of a crystalline particulate as the culprit. Lab scale testing using potential prefilter options showed that placing a 0.5-micron high-capacity PES prefilter in front of the 0.22-micron sterilizing filter could extend the life of the filter by approximately three times. This was more than enough to accomplish their goal of processing a full batch without filter changes. The customer purchased and installed HPPS-05-02 filters (0.5-micron prefilter over 0.22-micron sterilizing filter).
Critical Process Filtration Sterilizing Filter Options
Process Filtration offers the following choices for sterilizing filtration. All are validated for bacteria removal (0.22 and 0.1 microns), mycoplasma reduction (0.1 microns), and mycoplasma removal (0.03 microns).
SPS Filters (PES) & PNM Filters (Nylon 6,6) - single-layer membrane filters for maximum flow.
PPS Filters (PES) - Double-layer membrane filter (same pore size) for maximum protection.
DPPS Filters (PES) - Double-layer membrane filter with a bioburden reduction membrane in front of the sterilizing layer to increase life where high bacteria counts are present.
HPPS Filters (PES) - Double-layer membrane filter with a high capacity prefilter in front of the sterilizing layer to increase life where high particle load is present.
SPC Filters (single layer) & PPC Filters (double layer) - Positively charged PES when removal of endotoxin is required.
PNC Filters - Positively charged Nylon 6,6 for endotoxin removal where PES compatibility is an issue.
PTR Filters (PTFE) - Tank vent and process gas filtration.
Summary and Conclusions
So, we see that choosing the best sterilizing filter requires careful consideration of your filtration goals and process fluid characteristics, as well as identifying any issues with filters you may already be using. In many cases, the answer can be determined based on a basic process evaluation. In other cases, testing may be required to optimize the filter(s) to be used to best suit your application. In either case, the Critical Process Filtration Applications team stands ready to help.
CPF is a mid-sized manufacturer whose founder spent over 25 years working for the largest global filter manufacturing companies and built Critical Process Filtration with a strong knowledge base and mission to address the market’s need for a high-quality product, service, and support, and the best lead times possible. The company’s products are sold through multiple sales channels, all of which are backed by the manufacturer’s quality assurance, testing, and support services. After 23 years, CPF has a strong record of shipping products faster than many well-known vendors and helping customers succeed in their businesses.
Are You in Need of Assistance in Sterilizing Filter Selection?
Critical Process Filtration's experienced Applications and Process Support staff will help you choose the best filter for your application, recommend a suitable equivalent if you are looking for a sterilizing filter replacement, perform any testing required to identify the right filters for your process, and help you determine how many filters will be required for your specific application. We can also assist in verification/validation of performance as required.