From a simple one-step operation to a complex process that includes other separation technologies, membrane and depth filters play a critical role in assuring contaminant removal.
Amelioration, Bottling, Cleaning, Process
Filtration is a key component in producing purified water used in food processing.
Working in conjunction with Reverse Osmosis
(RO), Distillation, Deionization (DI) and UV light systems, membrane, and depth media filtration retain microbes and particles in water that other systems either create or cannot capture. Process filters that remove
bacteria, mold, yeast, and endotoxins, as well as inorganic matter, add a level of retention and assurance that your water purification goals are met.
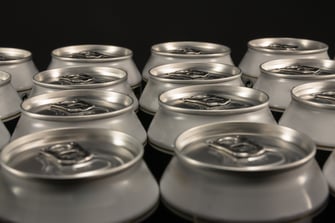
Critical Process Filtration provides cartridge, capsule, and lab-scale filters for the purification of water when your filtration goal is bioburden control, sterilizing, and/or fine and ultrafine particle removal. As a result, your water can achieve the necessary level of purity for bottling, amelioration, hydrating raw ingredients, cleaning process equipment, and filling applications.
These filters are installed in several locations along your process train to eliminate bacteria and remove the contaminants that discolor and change the taste of your final product. From the source (municipal, well, or spring) to the final filling machine, our water filtration products treat both liquids and process gases while also protecting tank contents.
Bacteria Filtration
When purified water products must be free of all bacteria, we recommend a filtration system that:
- Minimizes maintenance
- Creates barriers that prevent microbes and other organisms from entering via outside sources
- Implements strategically placed filters to capture bacteria at the point of entry and also in the final stages for added insurance
Since maintenance activity requires opening system components, the interior of the system is exposed to bacteria and other airborne organisms. If bacteria do invade, they’ll continue to grow and will contaminate anything downstream. Minimizing filter changeouts is done by utilizing prefilters and/or using high-capacity filters with longer life spans.
Creating barriers places obstacles in the way of bacteria and mold that might affect and potentially harm consumers and your brand. In addition to inhibiting organism growth with high temperatures and killing microorganisms using system sanitizing/disinfection with heat or chemicals, bacteria can be removed with membrane filters. Barrier options include: using pre-sterilized encapsulated filters as opposed to housings that are opened for cartridge filter changes; adding a tank vent filter to retain microbes that can enter as the tank pressure decreases; and filtering nitrogen/CO2 gases before filling tanks.
Designing a successful filtration train will require the strategic placement of the right types of filters. Critical Process Filtration’s products are optimized to meet your performance requirements. The placement of the expertly configured application filters coupled with the right economical prefilters will make all the difference in meeting your filtration targets both functionally and financially.
Sterilizing Filters
Microorganisms in food & beverage applications, include bacteria like Lactobacillus, but also molds like Aspergillus and yeasts like Saccharomyces that can be found in water. The best filters for bacteria removal are “sterilizing filters” made to pharmaceutical industry standards, usually with pore size ratings of 0.22 microns. A 0.22- micron pore is smaller than bacteria and will also retain the yeast and mold organisms mentioned above.
The most effective filter against bacteria in the water is constructed with a Polyethersulfone (PES) membrane because it delivers the best flow rate and throughput compared to other media. Critical Process Filtration offers several filters that are validated for use in liquid filtration. The challenge level is a minimum of 107 organisms per cm2 of filter media. CPF filters have > 7-log removal when challenged with the organisms listed below (0.10μm and 0.22μm meet the FDA definition of sterilizing grade filters).
0.10μm: Brevundimonas diminuta
0.22μm: Brevundimonas diminuta
CPF sterilizing filters (SPS, PPS, and HPPS) are optimized by the layering of media to enhance capacity and deliver high flow and throughput across a wide pH range. Each meets a specific filtration goal and comes in multiple configurations and device types. Capsules can be sterilized and high-temperature models are also available.
Bioburden Reduction Filters
When bacteria reduction is the priority and not sterility, highly efficient PES membrane filters are also the best means of reducing microorganisms and particles in the water. Contaminant load, particle size, and charge will determine the correct pore size and configuration (single or dual layer) of the filter. (Should chemical compatibility be a factor in the water purification process, Nylon media might be the better choice).
CPF’s integrity-tested BPS filter delivers high flow and throughput across a wide pH range for bacteria reduction. The BPS is available in a single layer or with an integrated prefilter layer for high capacity. It also performs as a prefilter to protect the final filter when used in sterile applications.
Endotoxin Removal Filters
When utilizing UV treatment in the purification process, endotoxins are commonly left behind. This negatively charged debris can be removed by implementing a PES or Nylon 6,6 filter with a positive charge. CPF’s PPC and PNC Filters are validated for absolute bacteria retention and remove endotoxins in one step. Our general service GPC Filter will remove endotoxins when sterility is not required.
The schematic below represents a basic overview of a water purification train and where filtration augments the greater process. In addition to ensuring purified water quality, the inclusion of process filters can lower your overall filtration costs by protecting the more expensive RO membranes with prefiltration, thereby extending their usefulness.
Particle Filtration
After Multi-Media Filters
Systems using well water or other raw, untreated water often use a multi-media filter before the water enters the treatment system. In some cases, multi-media filters are used with water from municipalities. These filters capture large particles but can release small particulates that should be removed with a particle filter before reaching downstream components to prevent clogging. Our NSPD filters consisting of polypropylene nano-spun technology capture contaminants from 0.5 to 100 microns.
Carbon Filters and Fines Trap
The Carbon filter shown in the diagram is typically a granular carbon filter that removes chlorine, chloramine, and other dissolved organic materials from the water supply. This protects downstream treatment components, particularly RO membranes, from oxidation. Unfortunately, carbon filters release fine carbon particles, so carbon fines trap filters are needed to protect downstream equipment. CPF’s FPD Filters are particle filters consisting of polypropylene depth media that comply with FDA requirements for food. The FPD filter delivers high throughput and pore sizes range from 0.10 – 100 µm. Our general service, economical GDMB Filter, utilizing melt-blown polypropylene media, can also be used for particle removal ranging from 1 to 100 microns.
Smaller systems utilize activated carbon block cartridge filters, such as Critical Process Filtration’s ACB Filter instead of granular carbon beds. Due to their method of construction, carbon block filters do not shed carbon fines after a short initial rinse, making a downstream filter unnecessary.
Resin Trap
The resin-based treatment process shown in the system diagram is a water softener. Removing hardness ions (calcium, magnesium, etc.) helps prevent premature fouling of RO membranes. The resin beads installed in softeners will break down over time and introduce resin fines into the water supply. Filters are used to trap the fines and prevent them from harming processes downstream. Polypropylene Depth filters are an effective and economical way to remove the fines early in the process. Critical Process Filtration’s FPD Filters, constructed with pleated polypropylene depth media, have a high retention rate ranging from 0.10 to 100-micron ratings. For very large particle loads, the HLP Filter made with a high loft polypropylene, will also deliver high retention at 0.10 to 10 microns.
RO Prefiltration
In most cases, the water entering an RO system is prefiltered to remove large particles greater than 1 to 5 microns, depending on the system. Removing these particles prevents premature fouling of the RO membranes which in turn reduces cleaning of the RO system, and protects the high-pressure RO pump. Choosing the right prefilter will depend upon the condition of the water before entering RO.
Water Tank Vents & Process Gas
Several methods are used to keep bacteria and other spoilage organisms from entering the system, including filtration of the air that enters tanks as they are emptied and the process gas that is used to fill the tank.
Tank vents allow air to flow in and out of the tank. As a tank is filled, the air inside is allowed to escape. When the tank is emptied, air (or a process gas such as nitrogen) is allowed to enter the tank to replace lost liquid volume. The air or gas entering the tank is filtered to remove particle and bacterial contamination.
Filters used for liquid applications are made of materials that attract water (hydrophilic) and allow the flow of water with low resistance. For air filtration, however, the media must remain dry. If the media becomes wet, and the pores are filled with liquid, the airflow is restricted and the pressure or vacuum inside the tank can reach critical levels and cause tank failure. Materials used in air filters repel water (hydrophobic) and resist wetting from water vapor or droplets.
To retain airborne particulates or bacteria CPF’s PTR Filter, constructed with a hydrophobic, .22-micron Polytetrafluoroethylene (PTFE) membrane is validated to sterilize process gas and the air entering the tank.
Support for Designing Your System
If your operation is purchasing purified water the expense alone may have you consider a water purification system onsite. A risk analysis by your team will determine the feasibility of that project.
If you are considering ways to improve efficiency and lower the overall costs of your existing system with filtration, we can help. Critical Process Filtration’s application engineers can evaluate your current system and make recommendations that lower your risks and assure your water purification goals are met.